R&D-
Technology
Steel
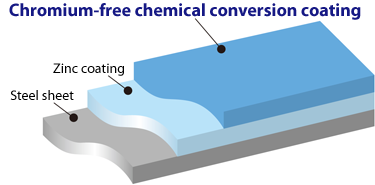
Steel has the drawback that it is prone to rust, and it is the mission of Nihon Parkerizing to protect steel from this corrosion. In recent years, in addition to the properties of corrosion resistance, workability and anti-fingerprint property required for the environmentally friendly chrome-free conversion films, there has been demand for additional value-adding functions such as conductivity, heat dissipation and scratch resistance. We are pursuing research and development into optimal environmentally friendly type multi-functional surface treatments for galvanized steel, galvanized/aluminized steel sheet and tin coated steel sheet used in household electrical appliances, automobiles, construction materials and beverage cans.
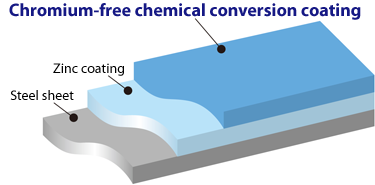
Automotive
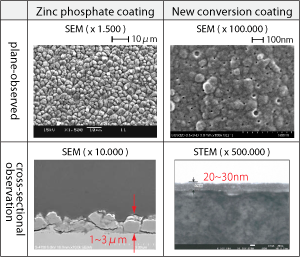
Our main focus is the development of surface treatment chemicals and surface treatment systems for automotive bodies and parts which primarily utilize cold rolled steel and galvanized steel materials. In the automotive surface treatment process which consists of degreasing, surface conditioning, phosphating treatment and electro-deposition (ED), nowadays there are escalating requirements not only for quality but also for process shortening, reduction of the environmental load and cost reduction. We have been working hard to meet the various needs of our customers, and have succeeded in completing the development and commercialization of new technology which is an alternative to the phosphate technology, and makes it possible to eliminate the surface conditioning process and lower the coating weight, as well as generating less sludge. Furthermore, as the trend towards making vehicles lighter in order to contribute to a reduction in CO₂ output and improved fuel efficiency has been ongoing and the variety of materials used has increased, we have been continuing our development work with the aim of providing ever greater added value technology.
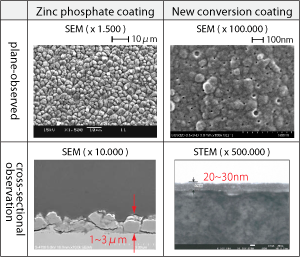
Non-ferrous metal
Beverage Can
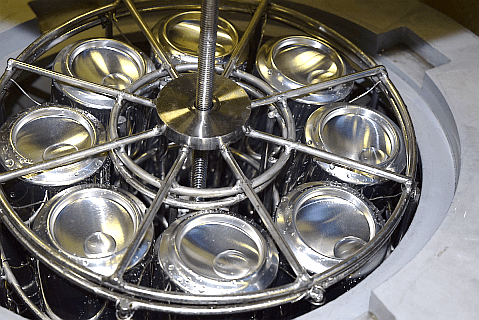
Nihon Parkerizing's surface treatment technology is also utilized on the ubiquitous beer and soft drink cans. Cans used for beer drinks are called D&I can and produced around as many as 1,500 cans per minute. The D&I can that has undergone high speed forming from sheet material is covered with oil from the processing as well as abrasion powder, and these must be thoroughly removed. After undergoing conversion coating which ensures corrosion resistance and paint adhesion, the can is printed with colorful designs. It is imperative that cleaning is done thoroughly at a low temperature and in a short time, and that the can bottom does not change color (corrode) in the sterilization process. In order to meet these requirements, we are engaged in research and development of surface treatment chemicals.
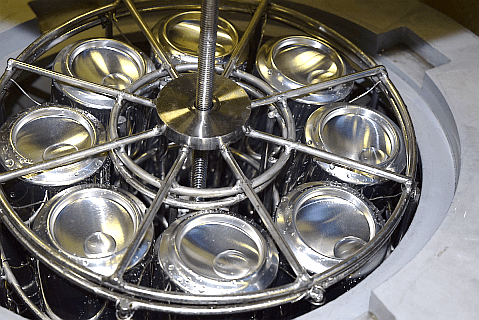
Car Evaporator
Car evaporator is the indoor heat exchanger to be mounted in the car air conditioner. In order to control the reduced heat exchange efficiency brought about by condensation on the fan during running of the air conditioner, as well as corrosion, decay, water splashing, noise and other nuisances, and the unpleasant odors generated in the thermal cycling, Nihon Parkerizing is developing multi-functional surface treatments which provide properties such as corrosion resistance, hydrophilicity (wettability), anti-bacterial property and odor control. There are various types of odors generated by different causes such as dust, decay, refrigeration and absorption and we worked hard to develop test equipment to recreate and analyze these odors, and to balance hydrophilicity and other functions. Day in and day out Nihon Parkerizing is working on the development of surface treatment technology to create an optimal environment.
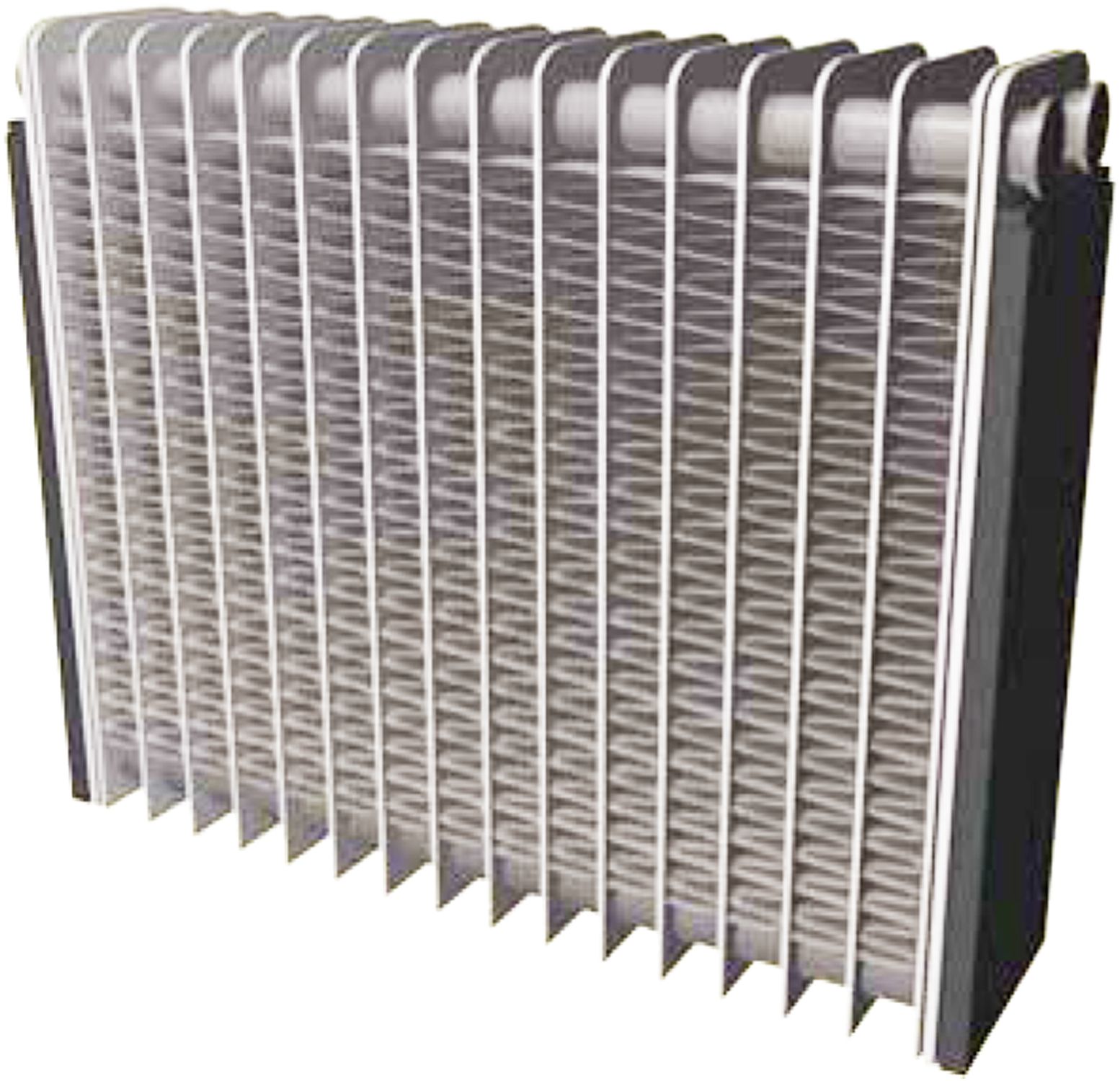
Advanced technology fields
Selective coating on comb substrate (PALMIC)
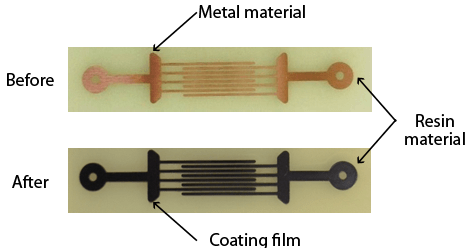
In recent years, the speed of technical developments in cutting-edge fields including information and communications, energy and catalytic substances has been increasing exponentially, and completely new and innovative technology is required in order to achieve commercialization of these new products. We are working on the development of multi-function surface treatments to meet the evolving needs of the market. For example, coating chemicals which provide insulation and thermal resistance properties to improve the electrical characteristics of motors and electronic parts materials. We are developing coating methods such as roll-on methods or selective reaction methods to enable the application of our chemicals in a variety of situations. Furthermore, we are working on the swift development of surface treatment technology with innovative functions in order to satisfy the needs of our customers.
Selective coating on comb substrate (PALMIC)
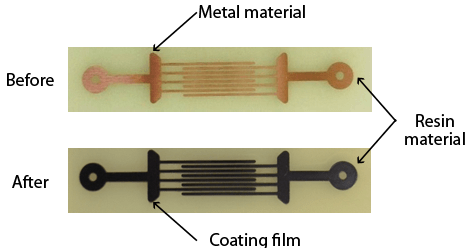
Cold Forming
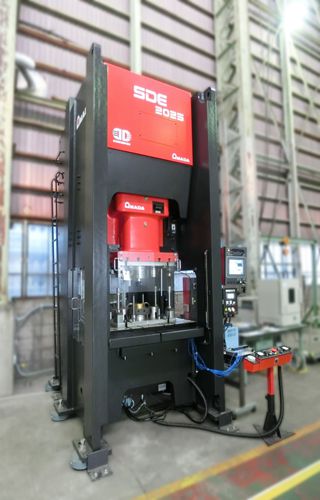
Servo press machine
Japan’s manufacturing technologies are supported by materials, and it is processing technology that makes the most of these materials. In order to develop the next-generation materials, suitable processing technology is necessary. Furthermore, it is lubricants that are critical for such processing technology. Our cold forming lubricants are widely used in the field of cold forming where it is important to reduce materials loss and conserve thermal energy. Nihon Parkerizing’s corporate philosophy is to contribute to the preservation of our global environment, and to this end, we are engaged in the development of next-generation lubricants utilizing our sophisticated array of testing equipment in order to keep one step ahead of the ever-changing requirements for processing technology.
Rolling Oil
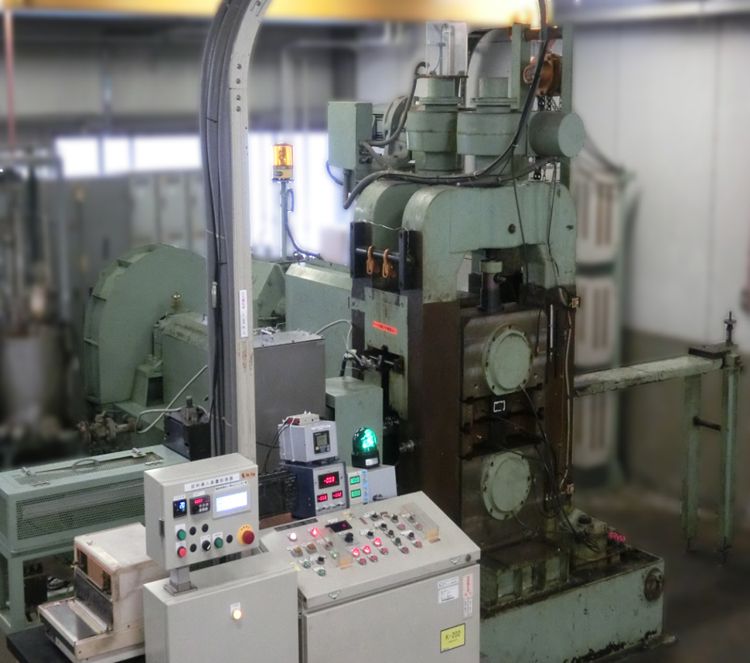
The metal materials that support the modern enriched lifestyles of our society have been processed in a variety of ways to render them suitable for use in automobiles, machinery and electronic equipment. For example, the rolling process whereby materials pass through two rollers to stretch and thin the metal sheet is highly efficient, and in the case of thin steel sheet, the rolling speed can reach up to 150km per hour. This kind of high speed rolling generates remarkable processing heat, and an excellent rolling oil is indispensable for preventing seizure of the roll and steel sheet to ensure stable and high quality rolling performance. In recent years, there has been increasing demand for rolling oil that can be used in even tougher conditions, and we have been pursuing research and development to replace the conventional technology with innovative technology that can meet the stricter requirements and is also environmentally friendly.
Fundamental research
The mission of Nihon Parkerizing is the creation of core surface treatment technology to support the next generation. We aim to further pursue and deepen the essence of the surface treatment technology that we have built up over the years. In addition, we are promoting technological fusion by gathering together researchers from different fields to develop the seeds of new technologies.
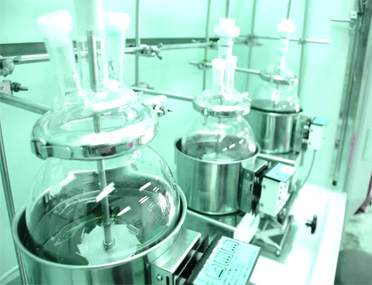
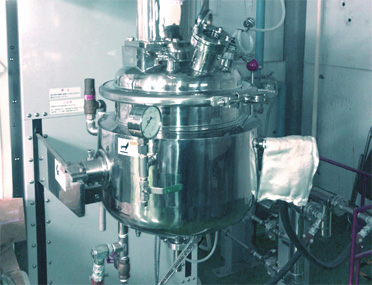
Analytical Science
In addition to quality, the requirements of the market have diversified in recent years to include a reduction of the environmental load, cost reduction and process shortening. Sophisticated analysis techniques are a key factor supporting product quality assurance and the development of surface treatment technology to meet the evolving requirements of the market. Our researchers make the most of the analytical skills that have been painstakingly polished day-by-day with the utmost discipline, in order to develop deeper knowledge and contribute to the creation of new technology.
X-ray photoelectron spectrometer
Nuclear magnetic resonance spectrometer
Raman spectrophtometer
Inductively coupled plasma atomic emission spectrometer
Surface Hardening
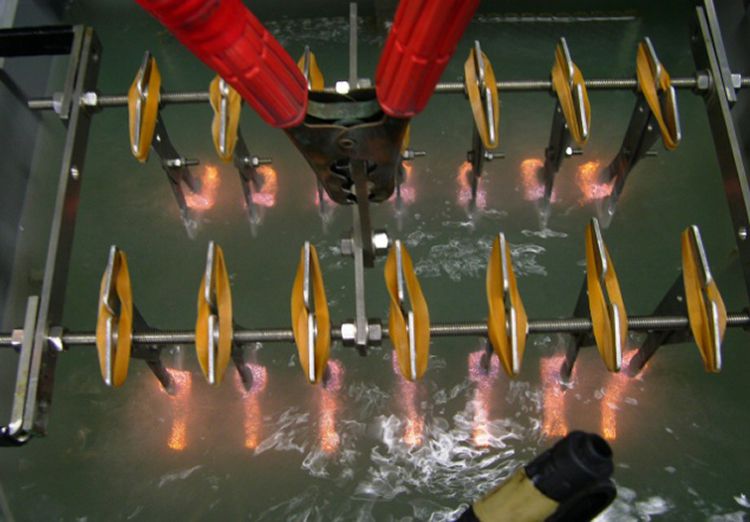
We develop surface hardening technology including nitriding and carburizing heat treatments, composite hard plating and plasma electrolytic oxidation(PEO). Among our heat treatments, we have established a salt bath nitriding method which is a low energy consumption, low cyanide type environmentally friendly technology. In our development of PEO, a method of hardening the surface of light metals, we have achieved a degree of surface hardness on aluminum for example which far surpasses that of hard anodizing, thus further expanding the scope of application of light metals particularly for use in auto parts. We will continue to pursue the development of new surface hardening technology which takes environmental issues into consideration.
Multiplex Surface Treatment
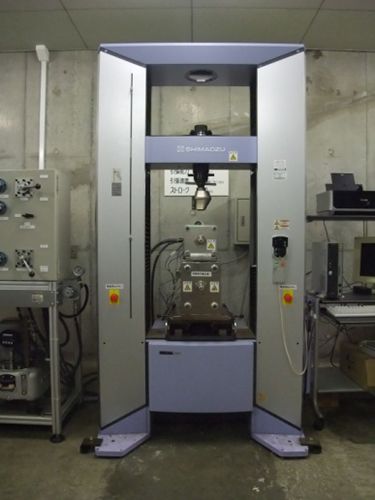
Multiplex surface treatment is a combination of processing treatments such as phosphating, Isonite (Nitriding which is a surface hardening heat treatment), or another specialized coating technology used to treat a wide range of metals, plastics or other materials to add surface functions such as corrosion resistance, adhesion, design features and lubrication. Our multiplex surface treatments are utilized in the automotive, electrical appliance, electronics and precision parts industries. We are engaged in the development of innovative and completely unique surface treatment technologies including ceramic films, extremely acid resistant coatings, extreme heat resistant coatings and other such cutting edge highly functional technologies.