ESG Information
Social Management of Chemical Substances
To fulfill our social responsibility as a chemical manufacturer that manufactures and sells chemical products, we have formulated a policy for the management of chemical substances in products and established a “Chemical Substance Management System (hereinafter referred to as CMS)”.
We collect, manage, and communicate complex and voluminous information on the hazards, toxicity, and risk assessment of chemical substances based on domestic and international laws and regulations, as well as customers’ standards, and share this information internally for CMS activities.
Policy for the Management of Chemical Substances in Products
At Nihon Parkerizing Co., Ltd., we have established and operate the Policy for the Management of Chemical Substances in Products below to fulfill our social responsibilities as a chemical manufacturer that manufactures and sells chemical products.
- Management and disclosure of information
We properly manage information on the danger, harmful effects, and environmental impact of chemical substances in products. We obtain information about the chemical substances in products, check the information against the relevant laws and information about danger and harmful effects, and adequately disclose information to customers. In addition, we promote the enhancement of customer satisfaction in response to requests from the market and customers in compliance with our chemical substance management standards. - Development
We conduct research and development to reduce environmentally hazardous substances and promote reducing toxic and environmentally hazardous substances in products. - Education
We educate employees on the necessity and importance of chemical substance management and the risks associated with handling chemical products. We promote this education so that all employees can share a common understanding. - Consistency
We promote consistent system operation for every stage of our business, from the purchase of product materials to storage, manufacturing, and selling. - Continuity
We constantly update information on danger and harmful effects, laws and regulations, and other matters and promote the operation of our Chemical Substance Management System while continuously improving the system to reflect reality.
June 27, 2024
Nihon Parkerizing Co., Ltd.
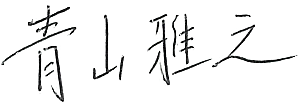
President
& Executive Officer
Structure and Management
For our CMS activities, we have established a structure in which the seven departments concerned to cooperate and collaborate under the supervision of management, the chief administrator, and the chemical substance control supervisor to manage the chemical substances in products. We have also made manuals and guidelines for responding to regulations, creating and issuing safety data sheets (SDSs), the voluntary management of chemical products and other matters, and engaging in activities following these manuals and guidelines.
Promotion sector
- Purchasing dept.: This department manages and evaluates suppliers. It operates and manages RMS activities under our own Green Procurement Guidelines.
- R&D: In the design, development, and improvement of products, this department uses chemicals as raw materials by confirming that they fulfill our Standards for Management of Chemical Substances in Products as early as in the procurement phase. It also understands the chemical management standards stipulated by customers and observes them in the design of products. Further, the department also promotes reducing toxic and environmentally hazardous substances in our products.
- Technological management dept.: This department has stipulated our Standards for Management of Chemical Substances in Products referencing the chemical management standards established by customers, laws, regulations in Japan, and other rules. It also checks the chemical substances contained in raw materials and determines the chemical compositions of products. The department uses those chemical compositions to create SDSs, Yellow Cards, and written responses to customer surveys on substances contained in products, among other documents. The technological management department also operates CMS activities and strives to promote and improve CMS activities as a whole on an ongoing basis.
- Processing and manufacturing dept.: This department has established control standards under which it takes measures to prevent the improper use of and contamination of products with chemical substances in the processing and manufacturing processes. It selects the raw materials of chemical products and the containers, packaging materials, and other matters under our Green Procurement Guidelines.
- The domestic and overseas sales dept.: This department keeps its eyes on the industry’s unique standards, such as the Global Automotive Declarable Substance List (GADSL), not to mention the chemical management standards established by customers, in its efforts to promptly update CMS activities. It provides customers with SDSs, which contain information about various laws and regulations, dangers, and harmful effects, and reports to customers the results of surveys conducted to identify whether products contain chemical entities, about which information was requested in its efforts to enhance customer satisfaction. The department also controls chemical substances for importing and exporting products and raw materials. In exports, it checks the standards and chemical substance regulations of the export destination countries, such as inventories. For imports, it ensures compliance with the laws and regulations of Japan submits notifications.
- Quality assurance dept.: In addition to responding to non-conformities, this department objectively evaluates the overall status of CMS activities. We conduct an internal audit led by the quality assurance dept. once a year. We report and review the results of audits and the activities of each department in an annual management review, aiming to improve CMS continuously.
- Environment and safety dept.: To ensure the safe handling of chemical substances at each of our business sites, this department researches the laws and regulations related to the safety of chemical substances contained in products and raw materials, provides corrective guidance, and provides training for the safe handling of chemical substances.
Input and Output of Chemical Substance Information
- Based on SDSs and other materials submitted by suppliers, we input information about chemical substances contained in raw materials into our Chemical Substance Management System. We input a wide range of information, including the names of substances in products, their quantities, harmful effects information, and inventories in each country overseas. Many of our products are mixtures of many raw materials, so we obtain and accumulate precise details on the individual raw materials. Thus, we clarify the information about the chemical substances contained in our products.
- A typical example of the information we output is the SDSs of our products. We create SDSs based on the information we input into our Chemical Substance Management System. When a customer requests that we find out if a particular chemical substance is contained in our products, we check the information in the system and give them a definite answer. We also respond in the same way to chemSHERPA (a common scheme for communicating information to enable the proper use of information about the chemical substances in products in the supply chain as a whole), which is operated and promoted by the Joint Article Management Promotion-consortium (JAMP) of the Japan Environmental Management Association for Industry.
Training Activities
Leveraging e-learning programs using our internal network, we improve employees’ basic knowledge and promote CMS activities through questions such as “What is a chemical substance?” “What is CMS?” and “What is SDS?”.
Activities for the Public
In June 2019, students from a nearby junior high school visited the Central Research Laboratories as part of a work-related learning program. We explained the CMS activities of Nihon Parkerizing to the students in a lecture titled “Chemical Substances and Our Life.”